Efficient teams deliver rapid service and create happy customers. The ideal situation. The wrong gloves can slow workers down, threatening your customer satisfaction. Here’s how:
1. Donning Gloves
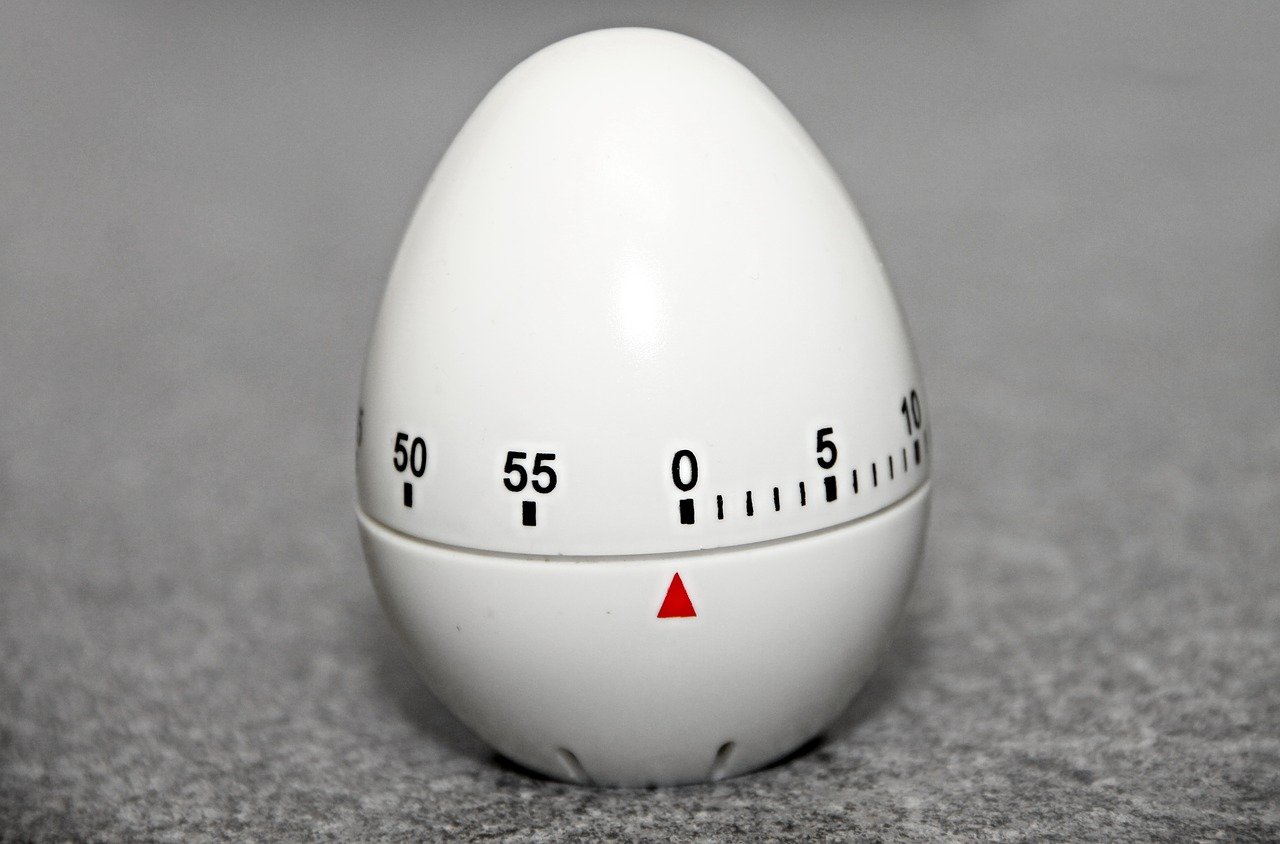
We hear it all the time. “I have to put on five gloves to get one to work.” Disposable gloves should not rip from simply putting them on. Your workers should be able to grab two gloves, put them on and get right to work. Repeatedly ripping, discarding and trying another pair of gloves adds unnecessary time to your process, slowing your business down.
2. Frequent Ripping During Use
Gloves are often cheap because they were made with inferior materials and manufacturing processes. Initially this may seem to boost your bottom line, but cheaply made gloves rip frequently and employees must stop working in order to change them. This reduces worker efficiency and increases the amount of gloves used, both negatively impacting your bottom line.
3. Hand Washing
Additionally, some safety protocols require workers to wash their hands between each glove change - adding to the time wasted discarding and donning new gloves. If your employees do not follow these guidelines, then cross-contamination can be a safety risk.
Whether it’s when you’re using them or when you are putting them on, a glove that rips is useless. Besides being a safety risk, ripping gloves decrease the quality and speed of service you provide your customers.
The Solution
Gloves should not rip during normal use. Don’t settle. Ordering gloves made with higher quality ingredients and manufacturing processes are a cost-effective decision.
Eagle Protect sources high-quality gloves, made the right way. Our team of experts is here to answer any questions you may have and help find the best glove for your business.
Want More?
Are you paying for ripped food contact gloves? Read more and find out.